The defects liability period (DLP) is the only time a capital project owner can lay claim to any unfinished, defective, and substandard quality work to be rectified by the contractor. The defects liability period is a fixed time, starting from the date of substantial completion also known as practical completion, during which the contractor has an express contractual right to return to the site to rectify defects. A typical DLP period lasts 12 months.
Any defects or faults that arise during this period are classed as obvious defects and are discovered by normal examination. Alternatively, these can be hidden defects that can only be discovered after a period of time, after usage and occupation, for example, due to defective materials or workmanship leading to water leakage. These defects must be put right by the contractor at the contractor’s own expense.
During the DLP, the contractor has the right to return to the site to rectify defects or complete unfinished work and the project owner is entitled to continue holding retention, to secure the contractor’s obligations in respect of incomplete or defective work. At the end of the defect’s liability period, the project owner will prepare a schedule of defects, listing those defects that have not yet been rectified, and agrees with the contractor on the date by which they will be rectified.
Using a Project Management Information System (PMIS) that has the functionality to manage completed project assets like PMWeb, the capital project owner can implement the DLP business process. This will enable managing, monitoring, evaluating, and reporting on the performance of this critical business process needed before issuing the project’s final acceptance certificate.
Similar to the Work Breakdown Structure (WBS) which is a must requirement to define, decompose and manage the project’s scope of work, the DLP requires having a Location Breakdown Structure (LBS) to define, decompose and manage the completed project’s assets. PMWeb allows defining all locations where the project owner might have real estate assets that are already completed and under operation, newly completed projects where the DLP to be managed, or projects that are still in progress. At each location, PMWeb allows defining the different buildings like for example Tower A, Tower B, Podium, External Facilities, etc. In addition, each building will be detailed into floor levels (GF, 1st Floor, 2nd Floor, etc.) for which each level will be further detailed into spaces like apartment 101, Lobby, Elevator Lobby, Mechanical Room, etc. Further, at each space, PMWeb also allows defining the list of equipment and tenants.
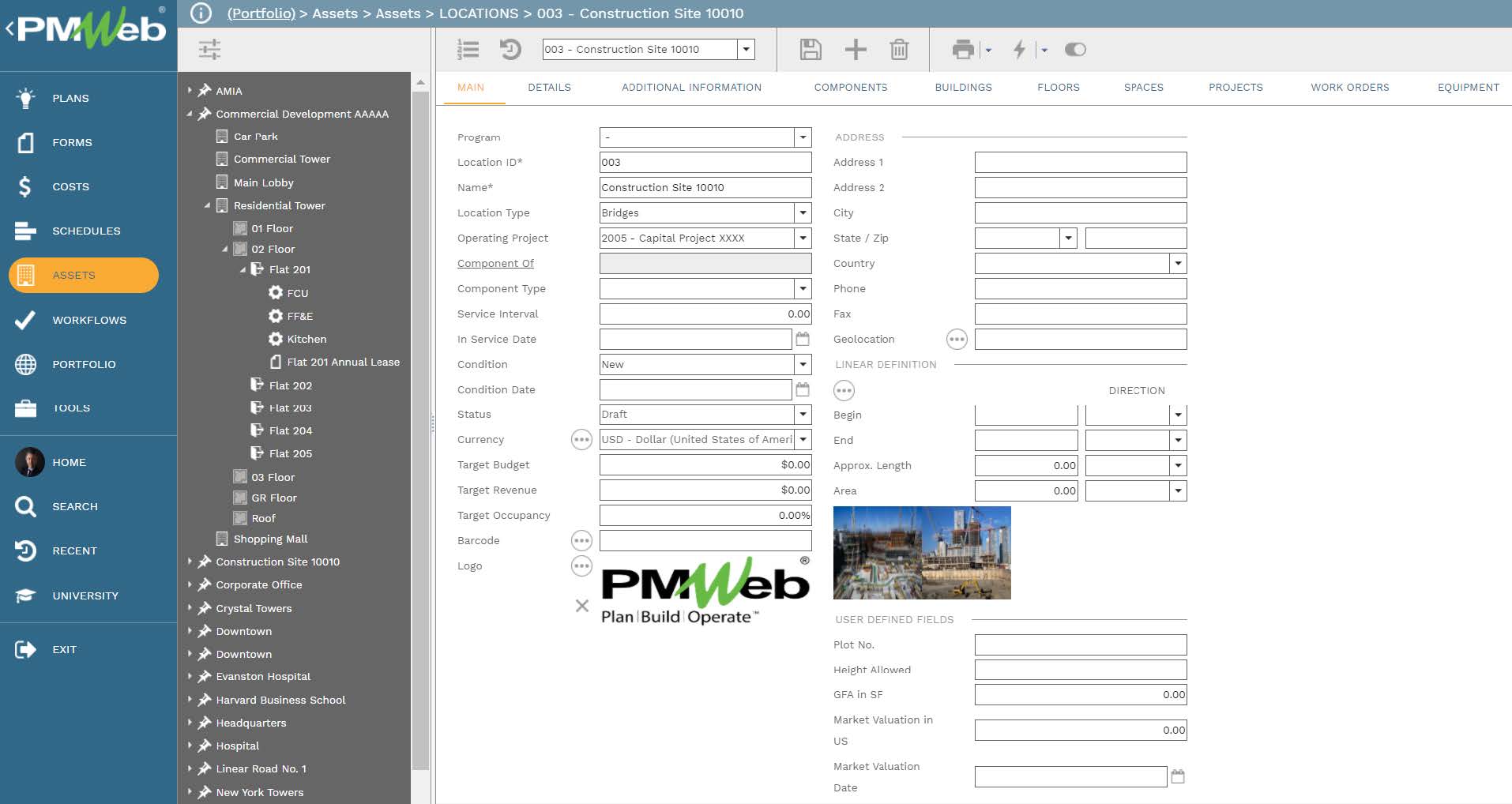
For each location, building, floor, space, or equipment, PMWeb allows capturing all possible details that a project owner might have including geospatial coordinates. The PMWeb additional fields option allows defining an unlimited number of user-defined fields that can be grouped by user-defined categories. Pictures for locations, buildings, and equipment as well as floor and space or apartment layout plan can be attached and displayed on the related asset definition page. Those pictures and documents will be usually uploaded and stored in the PMWeb document management repository.
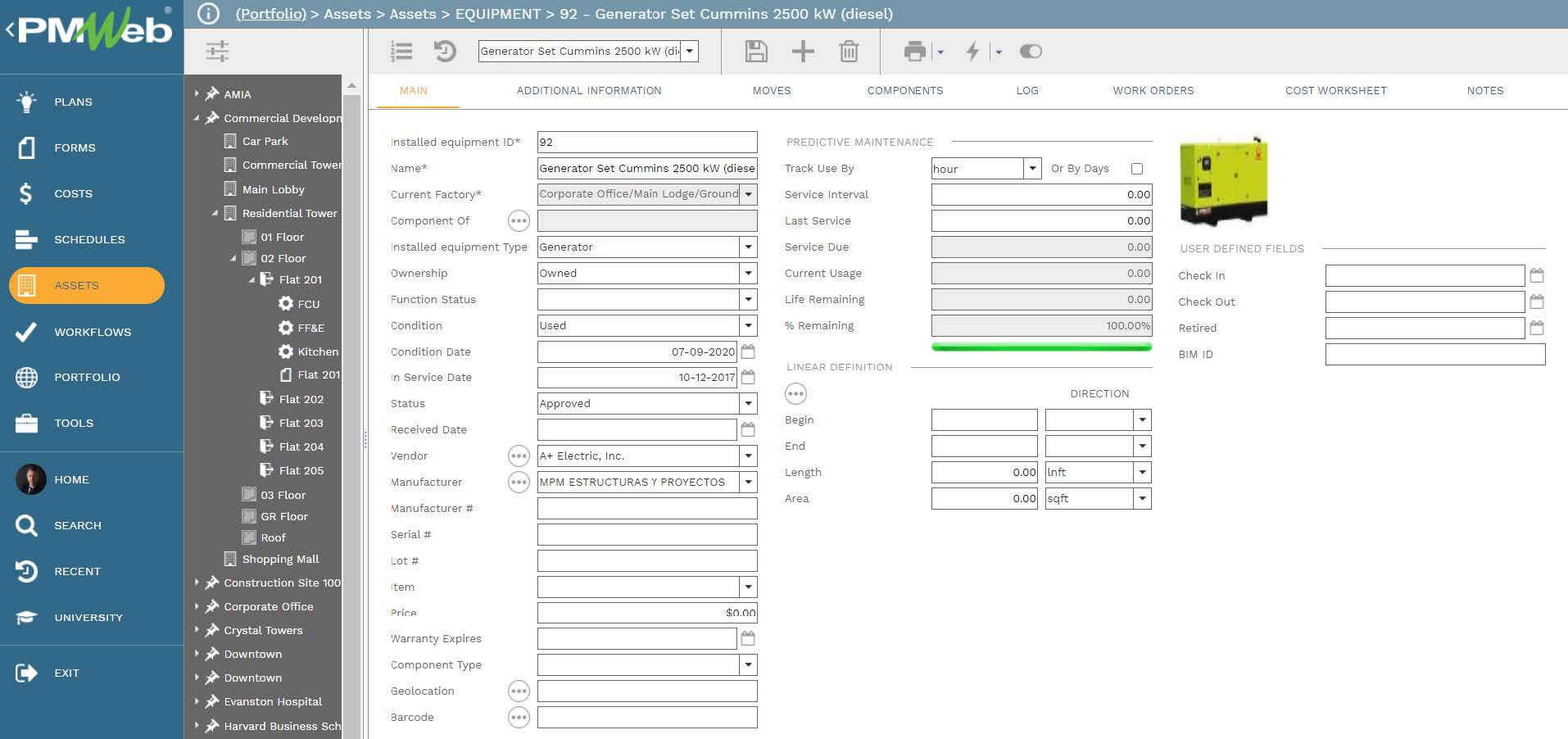
All discovered and reported defects will be brought to the attention of the project owner superintendent who will, in turn, direct to contractor to address the defect. The superintendent’s direction must be in writing, provide sufficient particulars of the defect and state a completion date (and ideally a completion time) for the rectification work. A direction that does not satisfy these requirements may not be effective.
The superintendent will use PMWeb Request Module to report all such defects. By default, the form allows capturing all defect details including a link to the asset that is related to as defined in the Location Breakdown Structure (LBS). The form includes fields to define the category and type of reported defect which will select the value from a predefined dictionary where both the project owner and contractor agreed to. The form also includes a field for the Work Breakdown Structure (WBS) level that that assets relate to. Additional fields can be also created and added to the work request form. In addition, pictures of the reported defect need to be taken and attached to the request for which it will be displayed. For work requests that are approved as defects that the contractor must rectify, a work order will be issued to the contractor.
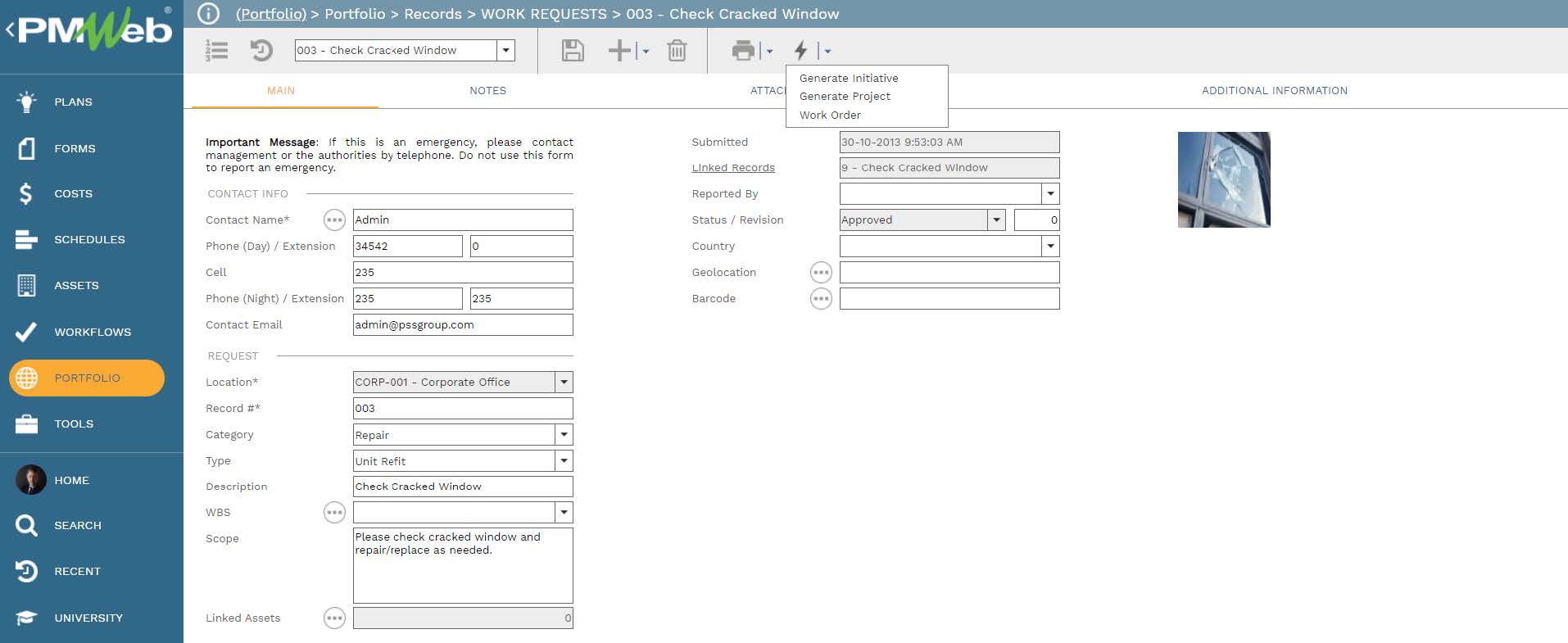
The reason for using the PMWeb Work Order module to manage the defects rectification process is that it provides better accountability when it comes to rectifying the reported defects. The data captured in the work request will include the data fields for Priority, Estimated Start and Finish and Approximate Duration, and other important data fields. Similar to other PMWeb modules, additional information data fields and groups are added to the Work Order module as well as attach all needed supportive documents including a picture of the rectified reported defect.
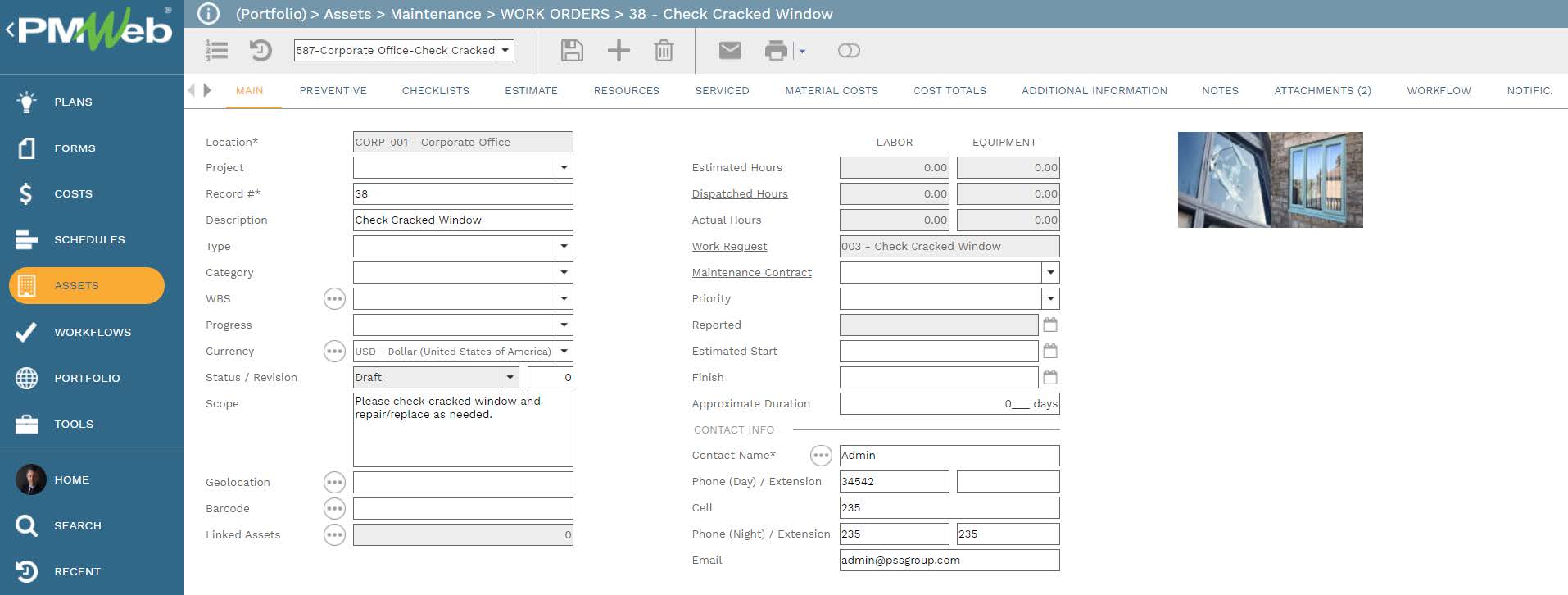
Nevertheless, what is important is that the work order module allows the project owner to capture the details of the estimated cost to rectify the reported defect in case the contractor refuses or delays rectifying the defect as instructed by the project owner. Those amounts will become part of the amounts to be deducted from the contractor’s final statement of account. PMWeb allows capturing all details needed for each cost item at the relevant Cost Breakdown Structure (CBS) level. Of course, the Work Order module also allows the project owner to capture the actual cost incurred in rectifying the reported defects. This will be usually the actual cost charged by the third-party maintenance contractor that the project owner had agreed with.
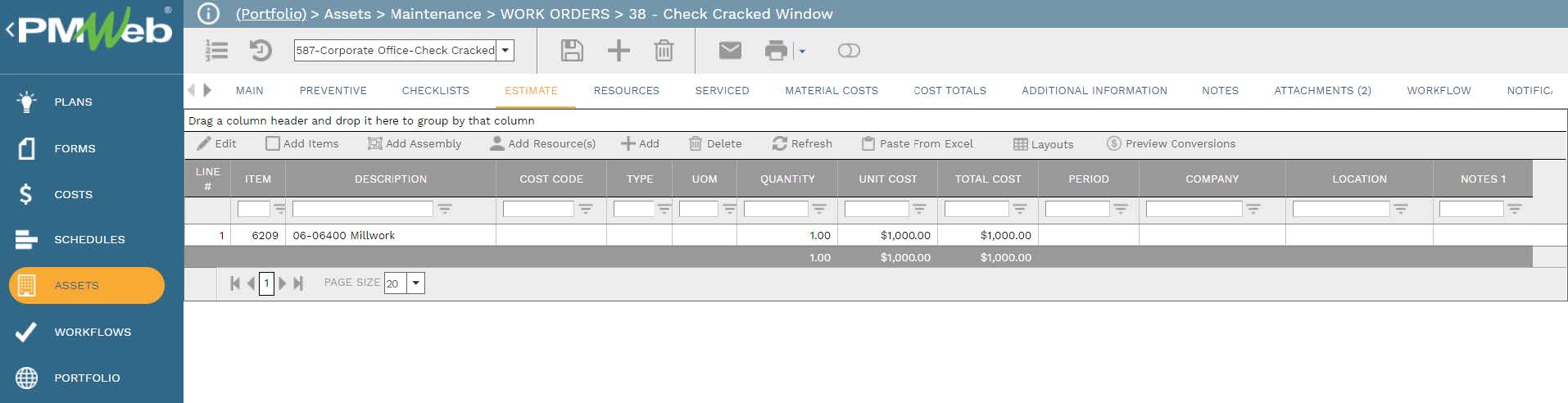
Further, PMWeb allows the project owner to capture details of the different maintenance contracts used to maintain the project owner’s own operating assets as well as work orders issued to rectify defects that the general contractor has failed or refused to rectify under the project owner requirements.

In addition, at the end of the DLP period, usually, subject to the construction contract agreement, a material stock or spare parts of between 10 percent and 15 percent is to be provided by the contractor in respect to tiles, granite, marble, door locks and handles, V-belts, smoke, heat and multi-sensor detectors, pull stations, manual call point, and paints, which might not be available in the market in the coming few years or a five- to eight-year period.
PMWeb inventory module will be used to capture the details of all those material stock or spare parts delivered by the contractor and for which they can be stored at different locations. For example, some of those inventory items could be stored at the building location itself, project owner warehouses, or even stored at the subcontractor’s or suppliers’ own warehouses if needed. PMWeb allows capturing the details of all consumed material stock or spare parts using the same Work Order module used for rectifying defects during the defect’s liability period.
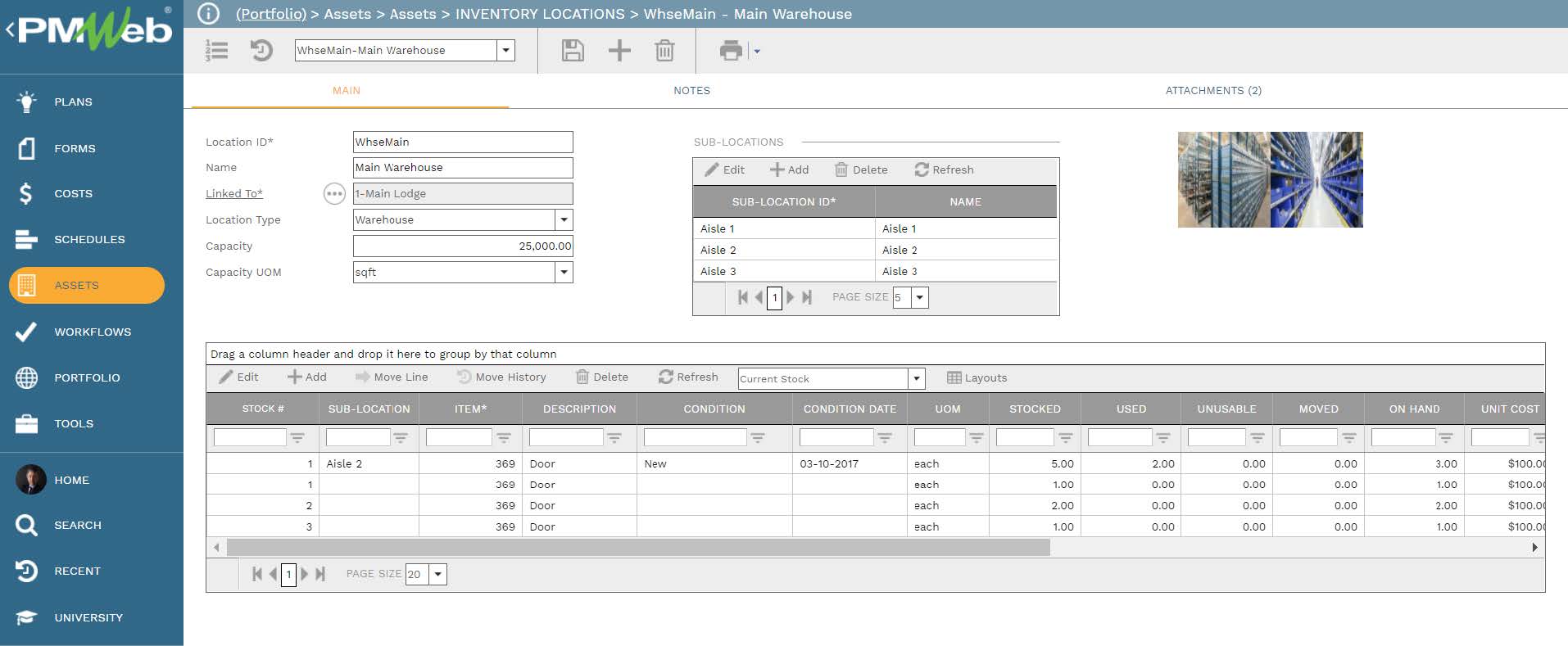
The data captured from the business processes used to manage the defects liability period will become available to be monitored, evaluated, and reported on. For example, a report can be generated to report on all defects identified by the project owner, contractor, tenants, among others. For each reported defect, the report will show the defect location, when it was reported, when the rectification process started and when finished. The report will also capture the details of the estimated and actual cost for defect items that a third-party contractor was used to rectify. The report will also include graphical visuals to summarize the details of the reported defect.
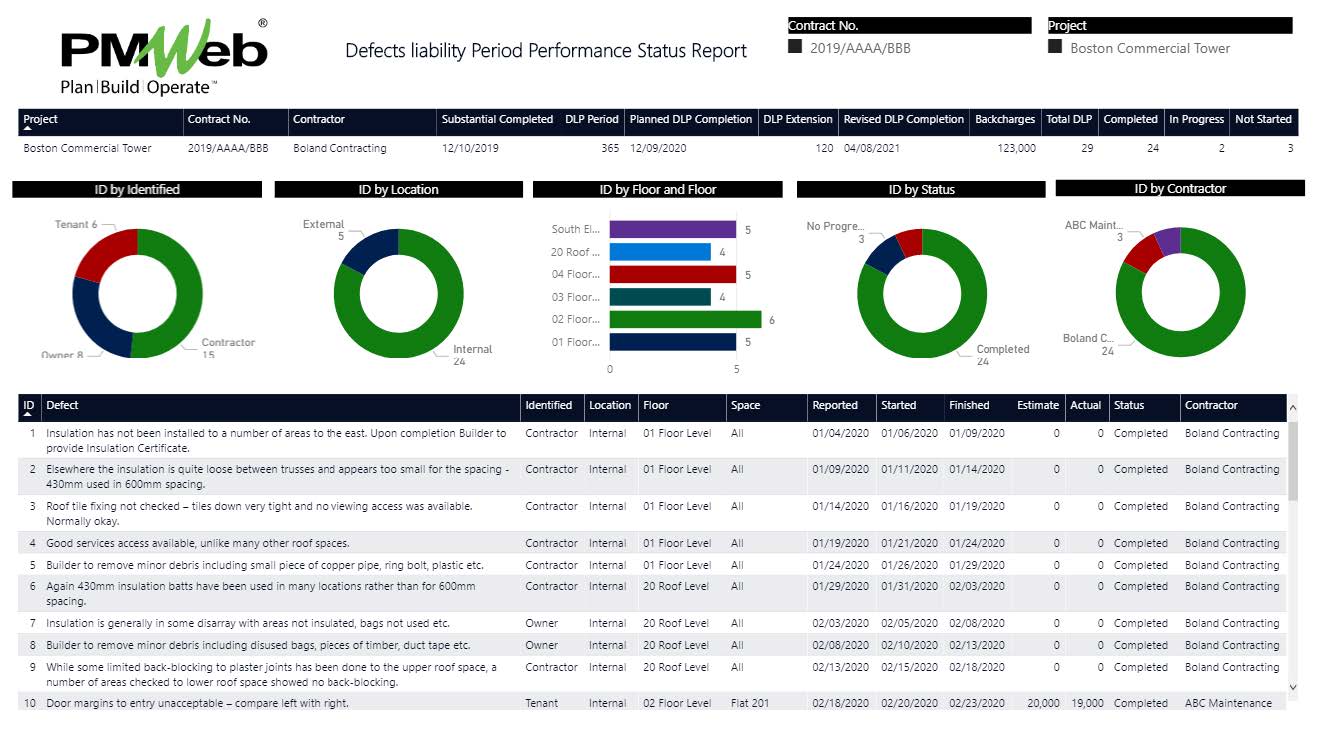