In our last article titled “The Earned Performance for Engineering and Procurement Deliverables on EPC and LSTK Contracts”, the level of the reported earned performance was set at the deliverable groups for each work package. The question is that can the same PMWeb Project Management Information System (PMIS) platform be used to formally document, monitor, evaluate and report the earned performance for the detailed procurement activities for EPC and LSTK contracts. The answer is for sure “YES”.
Using the same project, for each equipment that will be permanently installed on the project, PMWeb will be used to report the earned performance. For procurement items and where the COMPANY refers to the Project Owner, the earned performance will be reported against the tasks to Prepare MR/PR, Issue RFQ, Receive Offers, Complete Vendor Clarifications, Complete Evaluation & Submit TBE to COMPANY, Receive COMPANY Approval, Commit / Issue P.O., Receive & Approve Vendor Drawings, Place Sub-Orders, Receive Sub-ordered Materials, Complete Manufacturing, Complete Final Inspection, Complete Material Dispatch, Receive Material at Site and Prepare MRV. Of course, the COMPANY can elect to have different sets of earned performance tasks that will be specific for packages, equipment, or bulk items if this was a requirement.
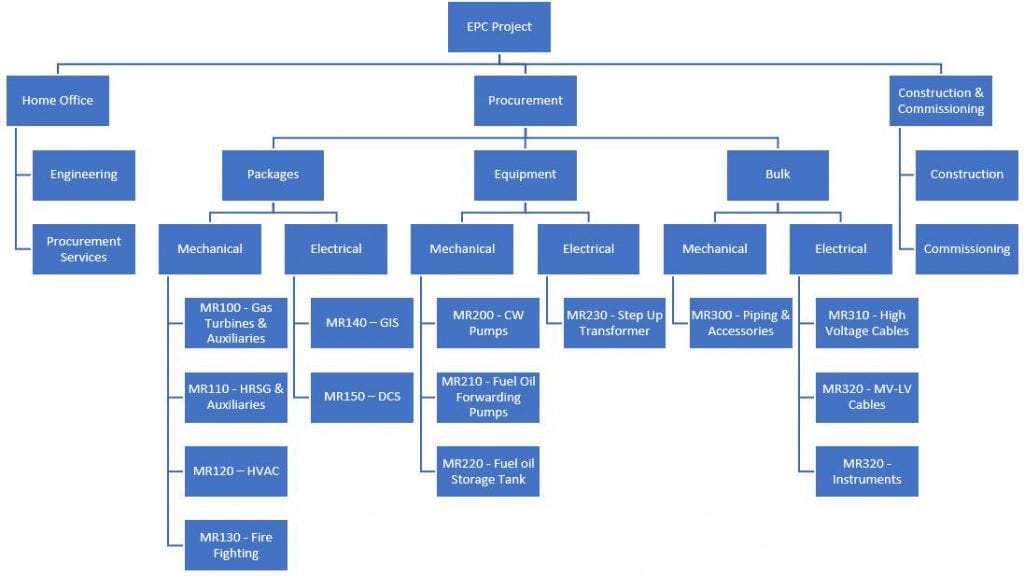
The same PMWeb modules used to report the performance of deliverable groups will be also used to report the detailed performance of equipment. Those were PMWeb modules for Commitment and Progress Invoices as well as Change Order if it was needed. Nevertheless, the improve the performance reporting, additional user-defined fields will be added to the commitment module. Those are the weight value that each deliverable group has, procurement group, system, and equipment type or category. Those three values will be defined in three separate selection lists to enable the PMWeb user to select a value from a predefined list of values. In addition, the default commitment type list will be appended with the value of “EPC Procurement Type”. In addition, the PMWeb users need to complete the fields for the shipping method and where the equipment to be delivered in case there are different possible delivery locations. Of course, there is no limit on the additional user-defined fields that can be added to PMWeb modules.
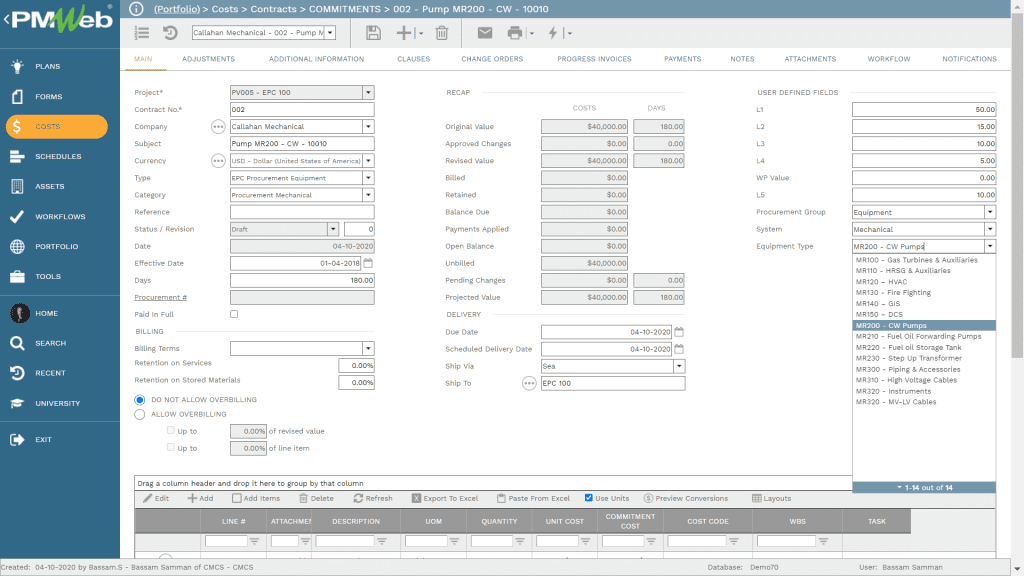
The detailed section of the commitment will include the procurement tasks along with the earned performance points that will be earned when the relevant task is completed. For each procurement task, the PMWeb commitment module allows capturing the relevant cost breakdown structure (CBS) level, work breakdown structure (WBS) level, the integrated project schedule activity number for the procurement task, and the manufacturer name which will be selected from the predefined companies list module. Of course, additional fields can be added if needed like for example, a field for the procurement task planned completion date.
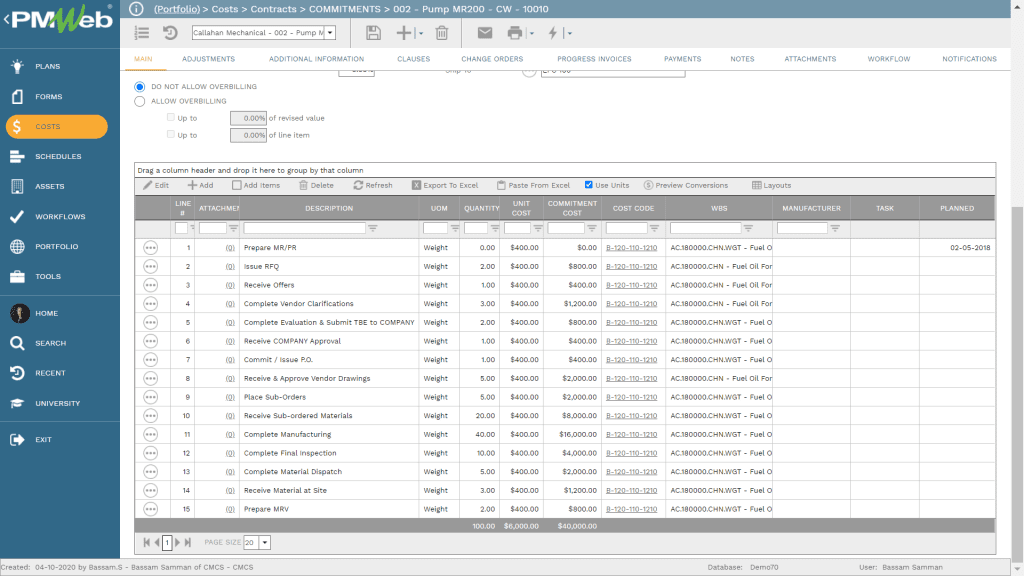
For each procurement task, PMWeb allows defining the period for which the procurement task performance will be earned. This option will be needed to generate the planned and earned progress curves if needed. This will be needed in particular for high-weighted procurement tasks that spread over more than a single period and for which partial progress earning is permitted.
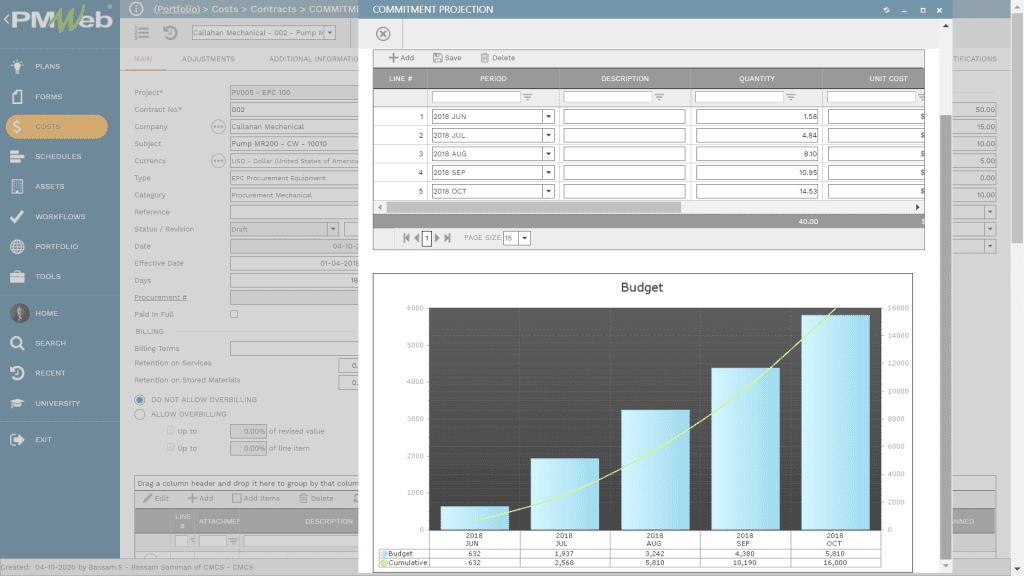
The execution of the equipment procurement will produce installation drawings, specifications, calculations, purchase orders, shipping documents, factory test results, custom clearance documents, delivery notes among many other documents. PMWeb document management repository will be used to create the folders and subfolders to upload and store those documents so they can provide the backup for the reported progress of works. It is recommended that there will be a separate folder for each procured package, equipment, or bulk items.
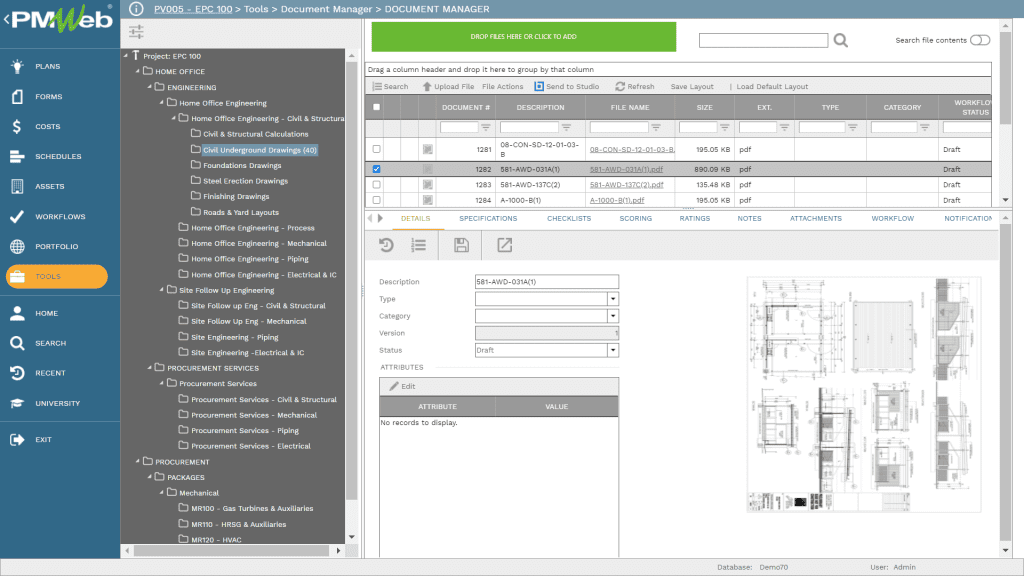
PMWeb progress invoice module will be used as the template for the Interim Progress Achievement (IPA) for each procured package, equipment or bulk items. At the end of each progress period, the assigned project team member needs to insert the percent complete value for each procurement task. This can be done manually or automatically by applying the percent complete value of the linked and imported project schedule activity. This will ensure full alignment with the project’s integrated updated project schedule. PMWeb will automatically calculate all other remaining field values for past period progress and remaining progress values.
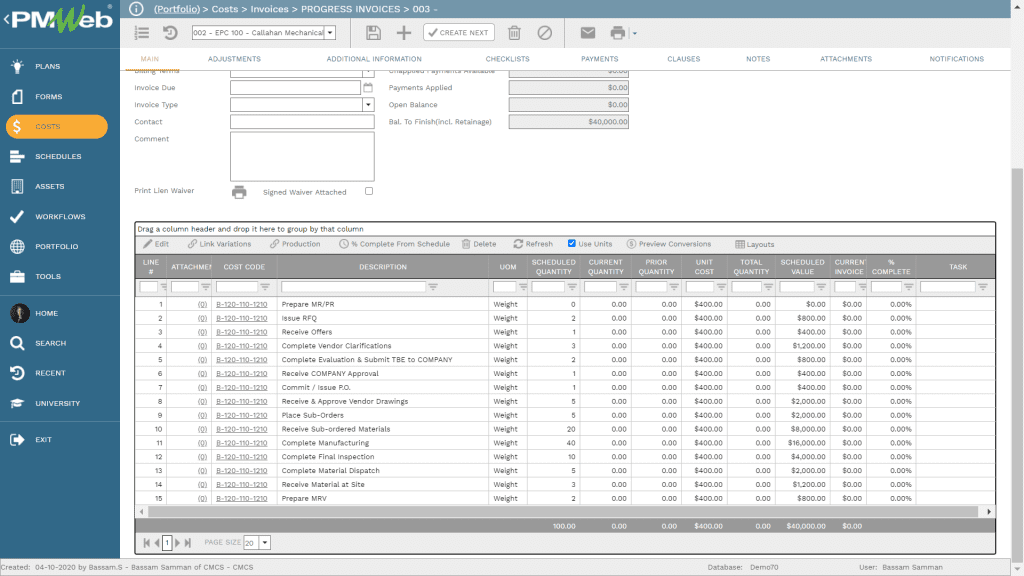
In addition, all documents produced for each progressed procurement task which have been uploaded and stored in the PMWeb document management repository, the project team member needs to attach to the relevant procurement task. Those documents could include installation drawings, specifications, calculations, purchase orders, shipping documents, factory test results, custom clearance documents, delivery notes among many other documents.
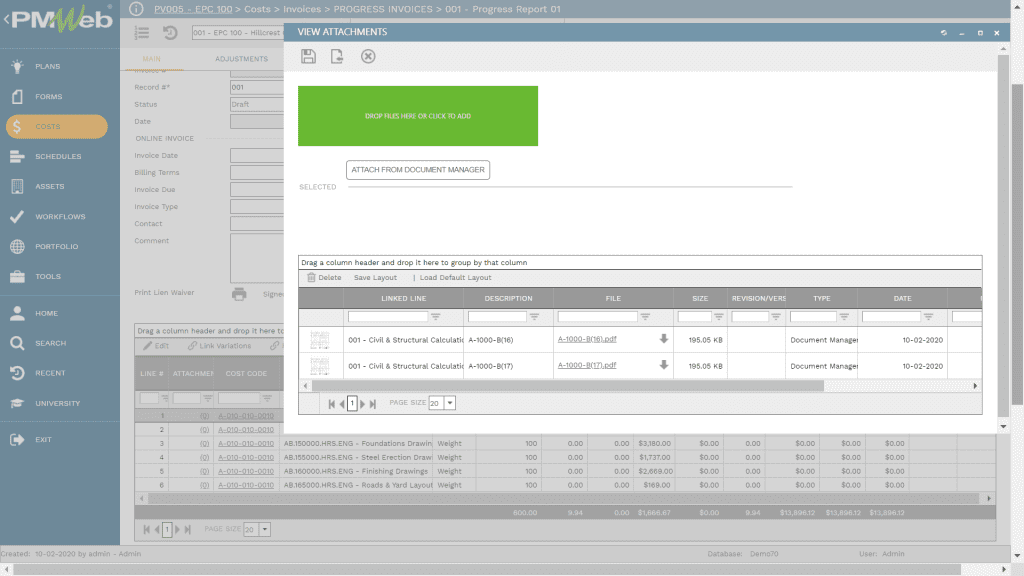
The above process will be repeated for each procurement package, equipment, and bulk item and for each progress period or when there is actual progress if needed. For the next period, the user needs to select the “Create Next” command to report the new period achieved progress. The captured progress for the period will calculate the total reported progress to date and balance to complete. Also, if the option of using the updated project schedule to report on the achieved percent complete values, then there is a need to import the updated schedule before applying the percent complete values. PMWeb schedule module will be used to import and maintain baseline and updated integrated schedule versions.
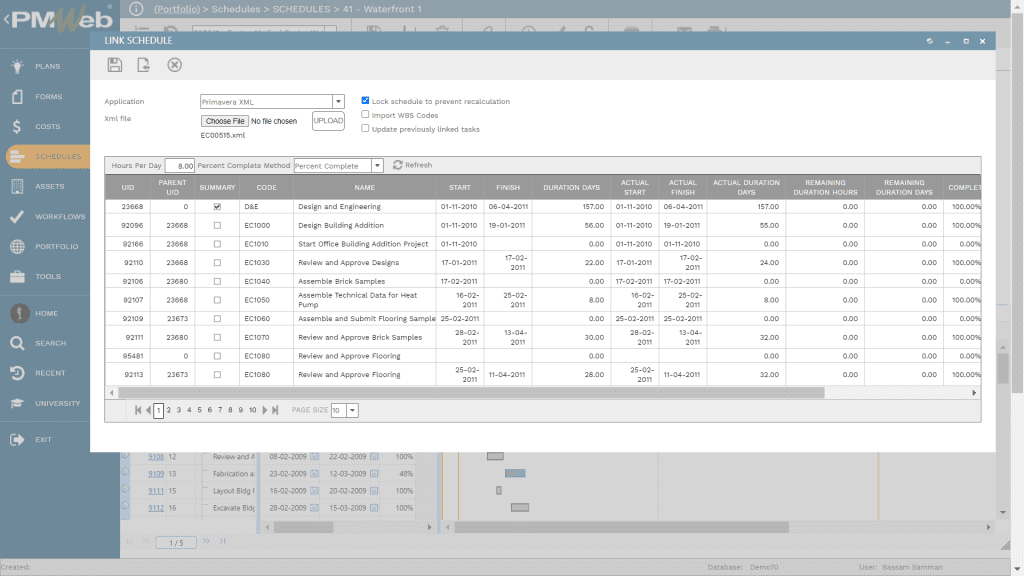
To formalize the creation of procurement packages using the commitment module and the monthly reported progress using the commitment progress invoice module, it is highly recommended to assign a workflow to each one of those two modules. PMWeb workflow will identify the workflow steps, duration, responsibility, available action types, and sequence. In addition, the workflow could include conditions to enforce the approval authority rights assigned to the project. For example, if the progress invoice total amount exceeds a certain value, then could require an additional approval level for the progress invoice.
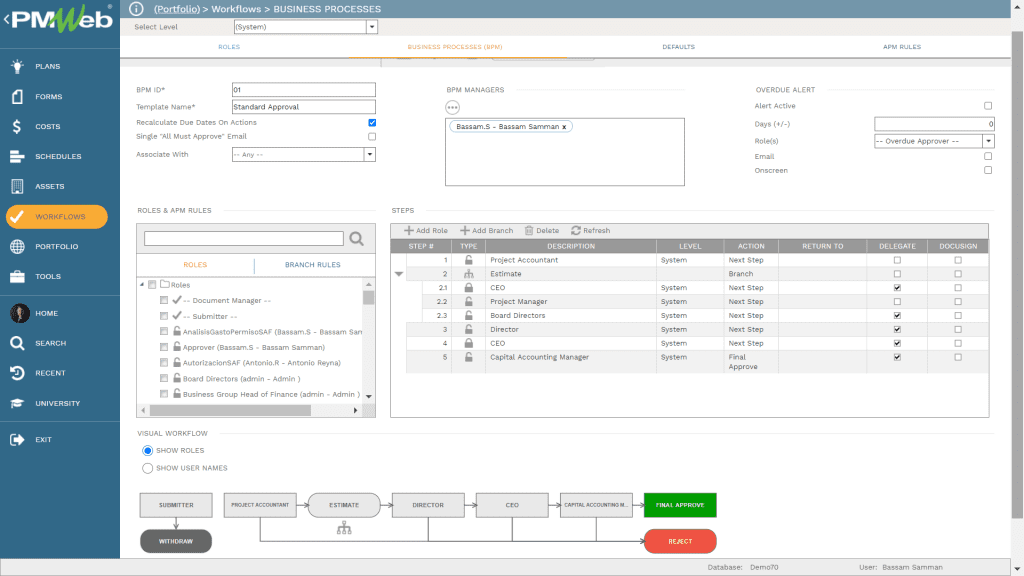
The information captured in the commitment and commitment progress invoice modules can be formally communicated by creating the needed forms and reports that will reflect the organization’s own branding and formatting requirements. In addition, PMWeb comes ready to use with many out-of-the-box forms and reports for all default modules including those two modules.
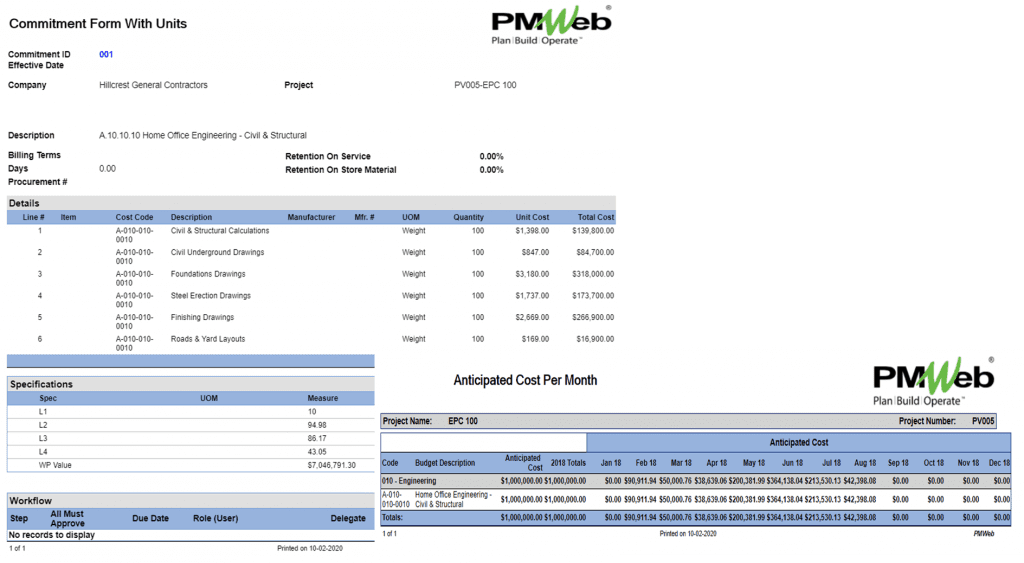
The PMWeb commitment change order module can be used to manage all changes that could occur for the planned procurement packages if this is a requirement. The change order module can be used to capture all changes that could have impacted the planned procurement tasks’ completion dates as well as change the assigned weight values for those tasks. A change order can be created from the work package commitment module by selecting the Generate Create Commitment Change Order command. A workflow can be also assigned to the change order module.
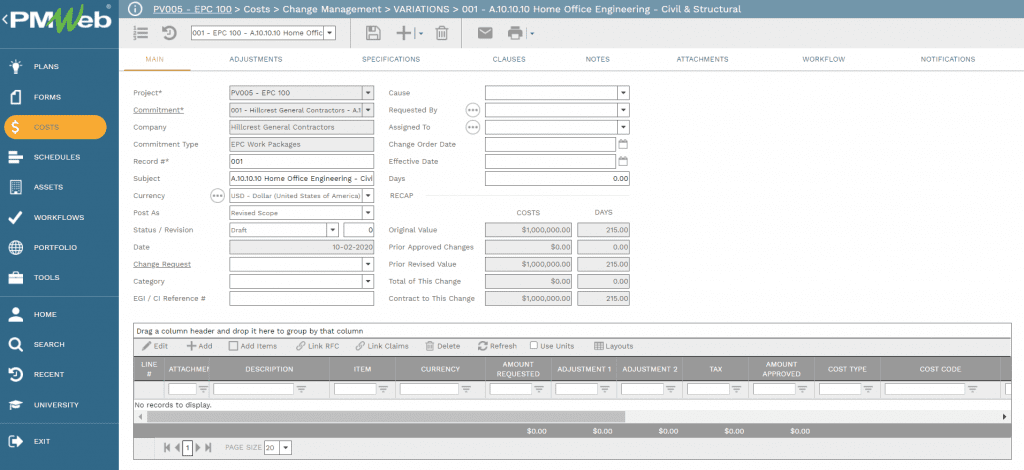
The trust-worthy, traceable and auditable information captured in the commitment and commitment progress invoice modules will enable the project owner and his engineering project management consultant (EPMC) to create real-time reports to provide a single version of the truth on the performance status of procurement packages, equipment, and bulks. Those reports are usually hyperlinked to their source PMWeb records to enable the report reader to drill down and have insight on what has been delivered, reviewed, and approved for the reported earned performance. As an example, the report below details all bulk, packages, and equipment to be procured on the EPC project. For each item to be procured, the report shows the dates for which the procurement progress will be earned. Those are the procurement tasks of Prepare MR/PR, Issue RFQ, Receive Offers, Complete Vendor Clarifications, Complete Evaluation & Submit TBE to COMPANY, Receive COMPANY Approval, Commit / Issue P.O., Receive & Approve Vendor Drawings, Place Sub-Orders, Receive Sub-ordered Materials, Complete Manufacturing, Complete Final Inspection, Complete Material Dispatch, Receive Material at Site and Prepare MRV. The report shows the assigned weight value for each item to be procured, planned progress earning for the elapsed period, actual earned progress, and progress variance.
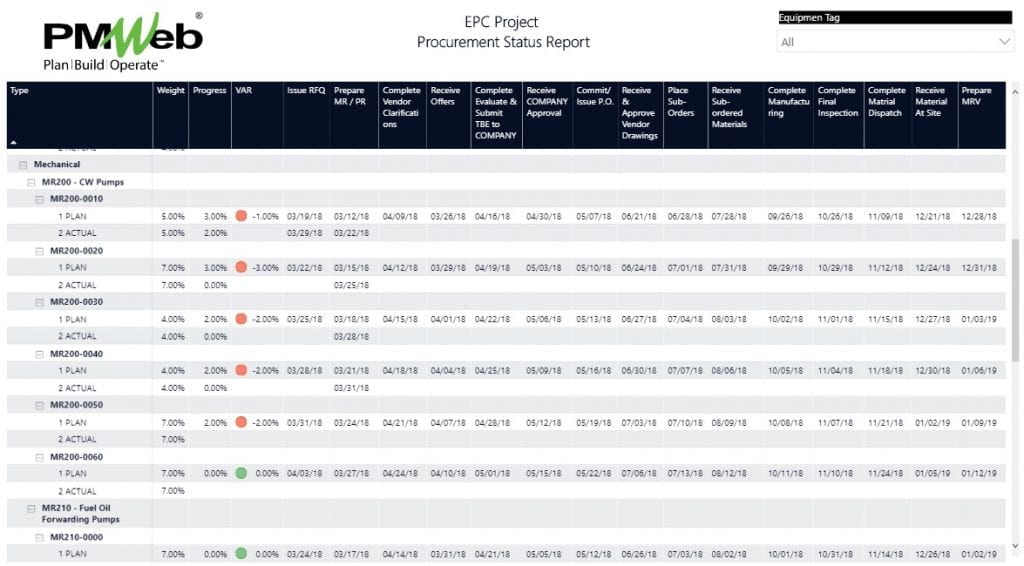