One of the key requirements that need to be managed, monitored, and reported on construction projects is the delivery, storage, and release of equipment and material at the different storage locations at the construction site. Those equipment and material items will be incorporated in the different building systems that are part of the project’s scope of work as well as some might be kept as part of the spare parts that need to be handed over to the project owner at the project’s completion as part of the basic and extended warranty requirements. For example, those equipment and material assets would include Air Handling Units, Fan Coil Units, Electric Distribution Panels, Pumps, Fixed and Loose Furniture, Bathroom Accessories among many others. Some of the delivered equipment and material could be procured directly by the project owner or by the contractors and his subcontractors.
The challenges in managing, monitoring, and reporting equipment and material deliveries on construction sites are many. One of those key challenges is how to keep track of, locate and secure the delivered and stored equipment and materials. Using Project Management Information System (PMIS) like PMWeb and IoT-based asset tracking technology like the one provided by Litum Technologies can provide a complete solution to keep a real-time, trustworthy, single version of the truth tracking of all delivered, stored, and installed equipment and material.
PMWeb Item module will be used to capture the details of equipment and material that will be delivered, stored, and installed. A new items folder will be created for each project to capture those items and their details including the RIFD tag identification number if available. Each project items folder can be broken down into subfolders to group items by the specification group that they belong to.
To expedite the process of creating the list of all equipment and material items that need to be managed and tracked, PMWeb allows importing those items and their relevant details from MS Excel. The item number will be unique for each equipment and material asset and the same item number will be used in the commitment contracts to capture the details of all ordered, delivered, and installed equipment and material items.
Of course, the defined item numbers are also used in other PMWeb modules like a cost estimate, pre-bid, online bid, procurement/bid analysis. This will provide the project team the ability to trace the complete history of all equipment and material assets installed, used, or stored on the project.
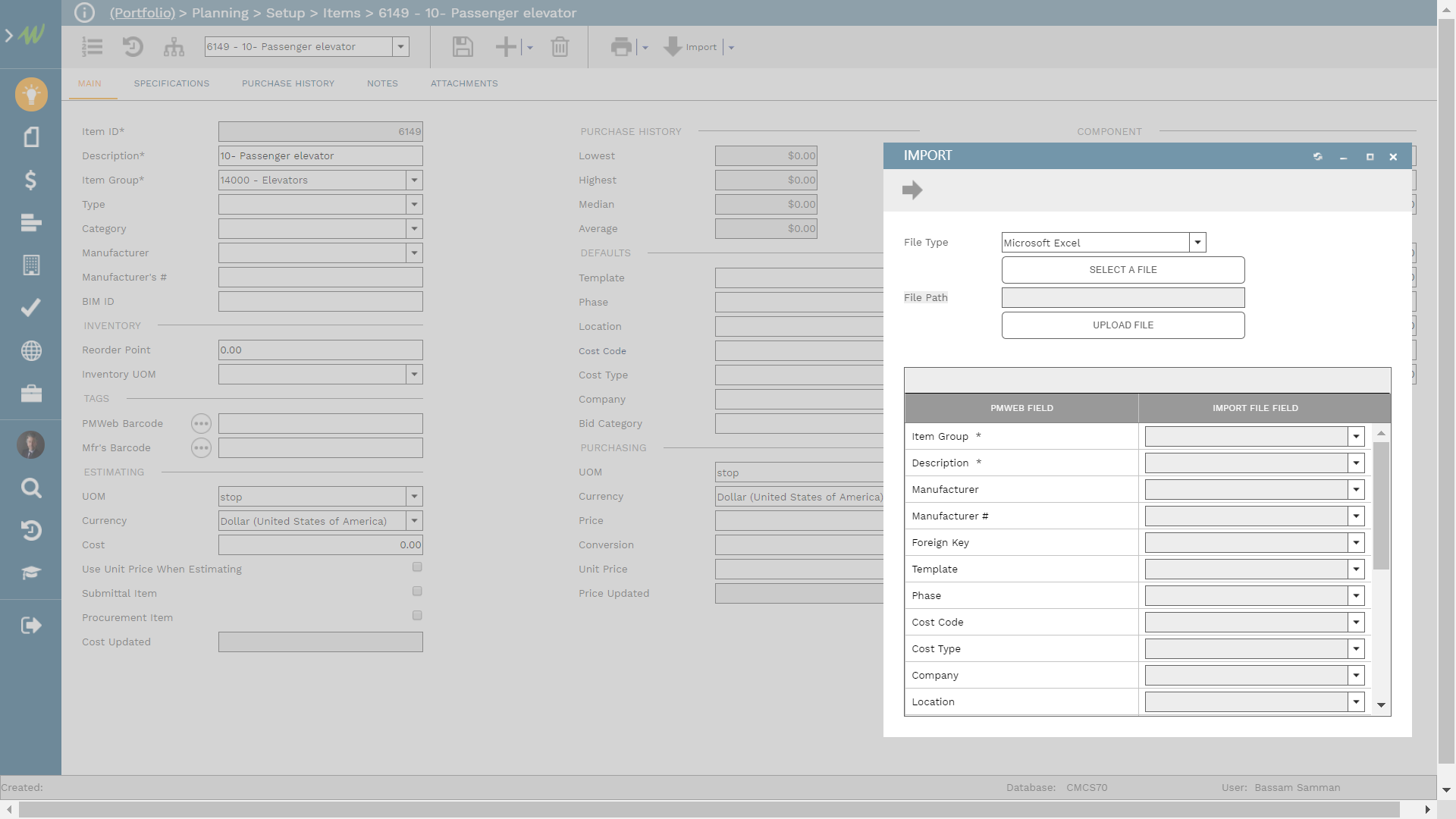
The added equipment and material items will be dragged and dropped into each commitment contract to capture the details of all items that will be procured through this awarded commitment which could be in the form of contracts, subcontracts, purchase orders, etc. This is necessary to capture details of interim payments made against delivered and stored equipment and materials and later when they are installed, inspected, tested, and commissioned.
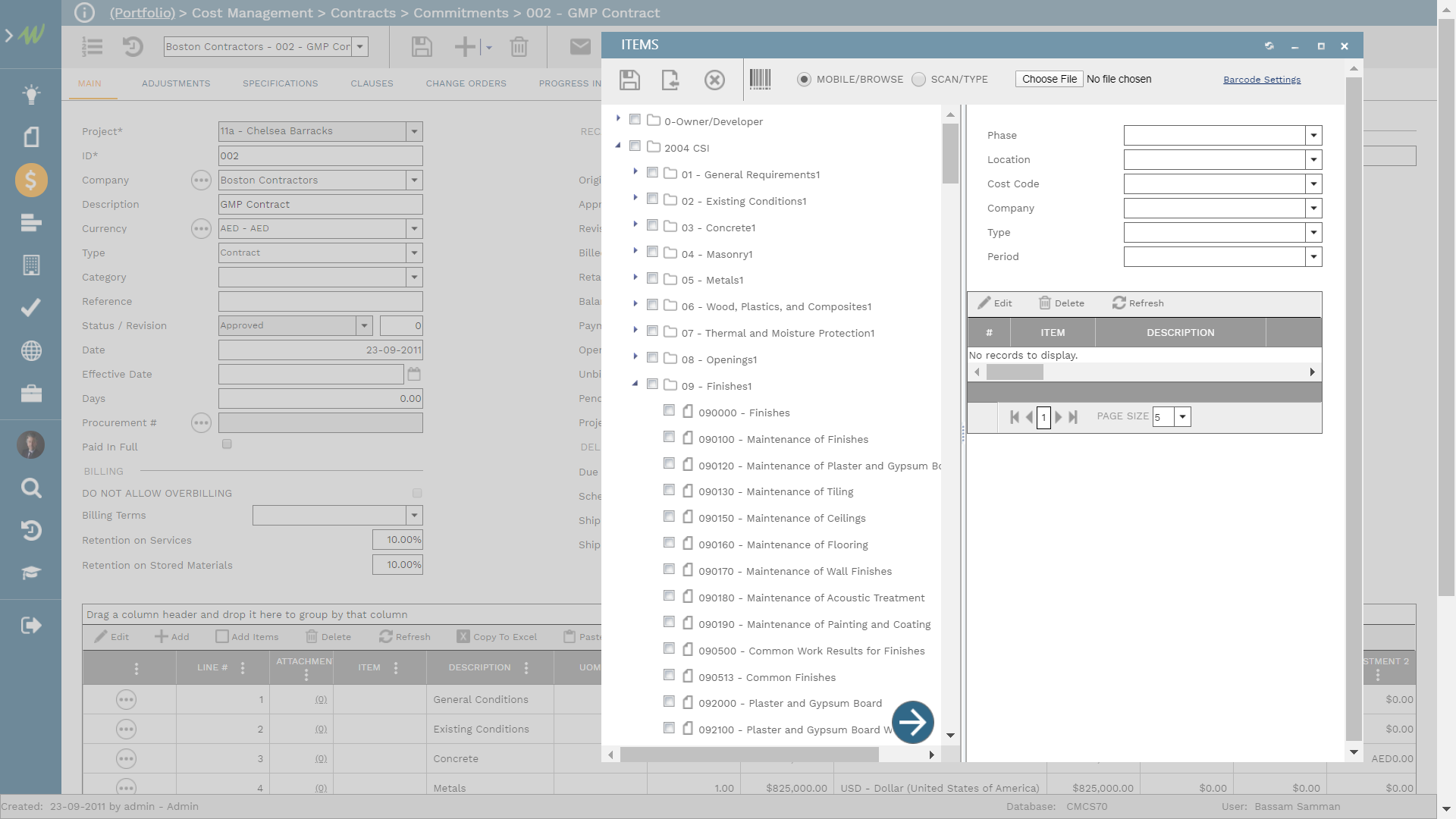
As the construction work progresses, the contractor will be required to maintain different storage locations within the construction site. Some of those storage locations could also include parts of the constructed facilities like the basement level as well as other levels. For each delivered equipment or material, an RIFD tag will be added. The items database should be updated with the RIFD tag identification number assigned to the delivered equipment and materials. Those RIFD tags will provide the real-time tracking of those assets, that is delivered equipment and materials. Litum Technologies provides the web-enabled platform to keep track of the delivered and stored equipment and materials. The floor layout for all storage locations will be uploaded into Litum, which could be in either Autocad or picture file format. Color zoning for the storage layout can be done within Litum if needed. This will enable navigating from one store location to another by selecting the relevant layout.
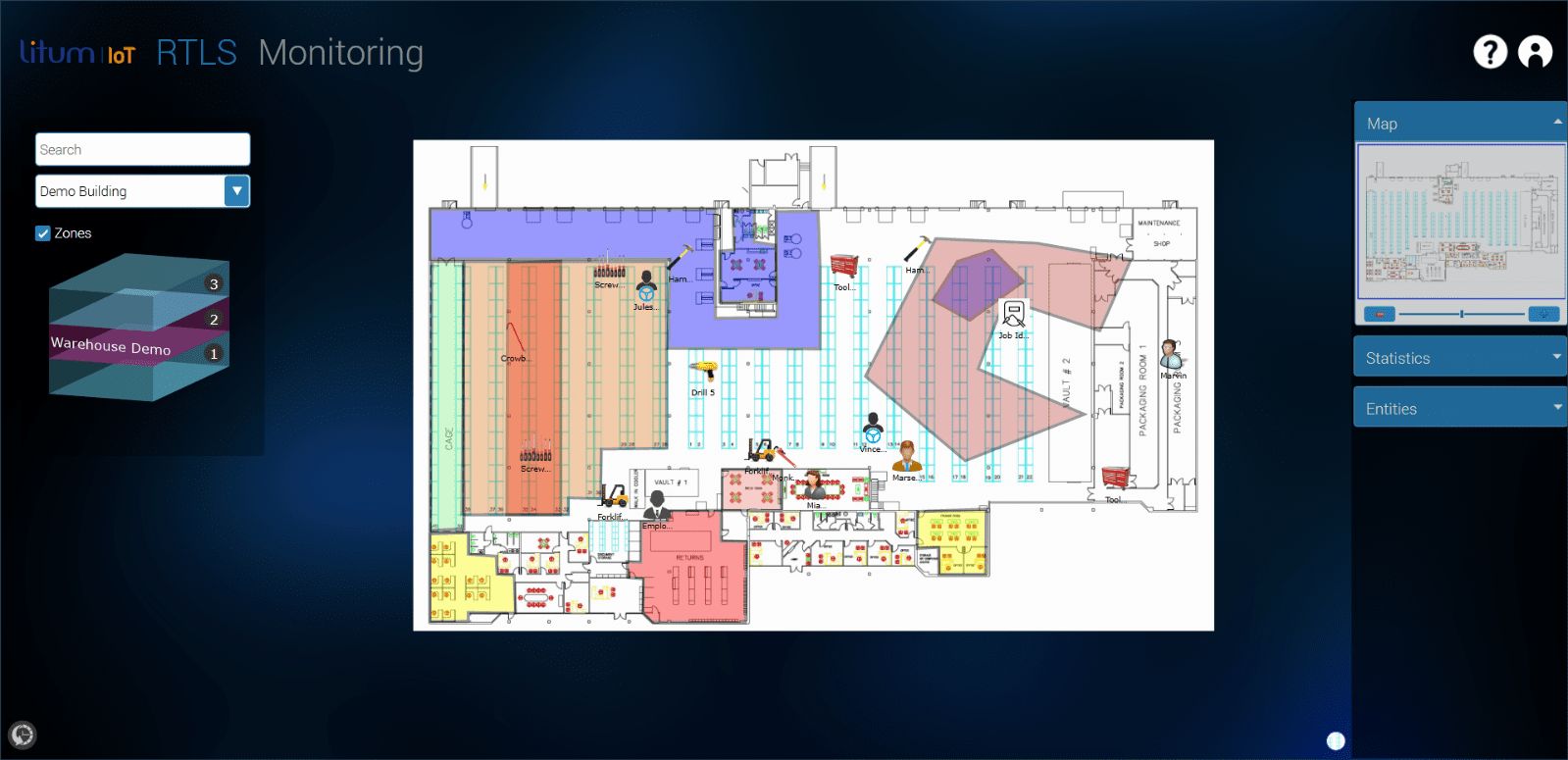
This will enable the project team to have real-time tracking of the location of all delivered equipment and materials as well as their movement history after they were first delivered. This is not only important to track where the asset is located as of now, but also to analyze the storage efficiency and the costs associated with relocating and re-handling originally delivered and stored assets.
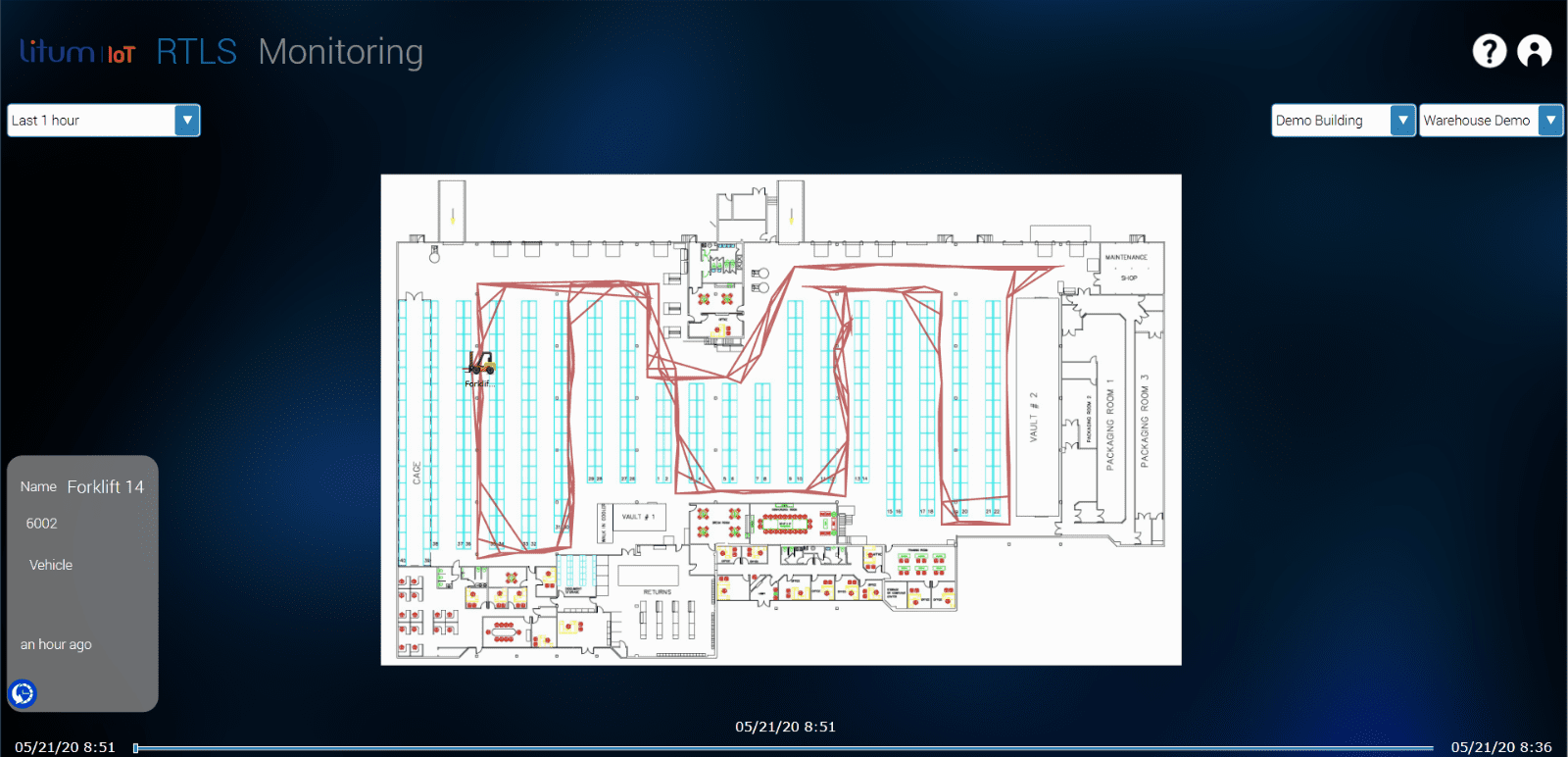
This information along with other information captured from RIFD tags assigned to labor and equipment resources will become available in the Litum Executive Dashboard. The dashboard can be modified to display the needed information in the desired format.
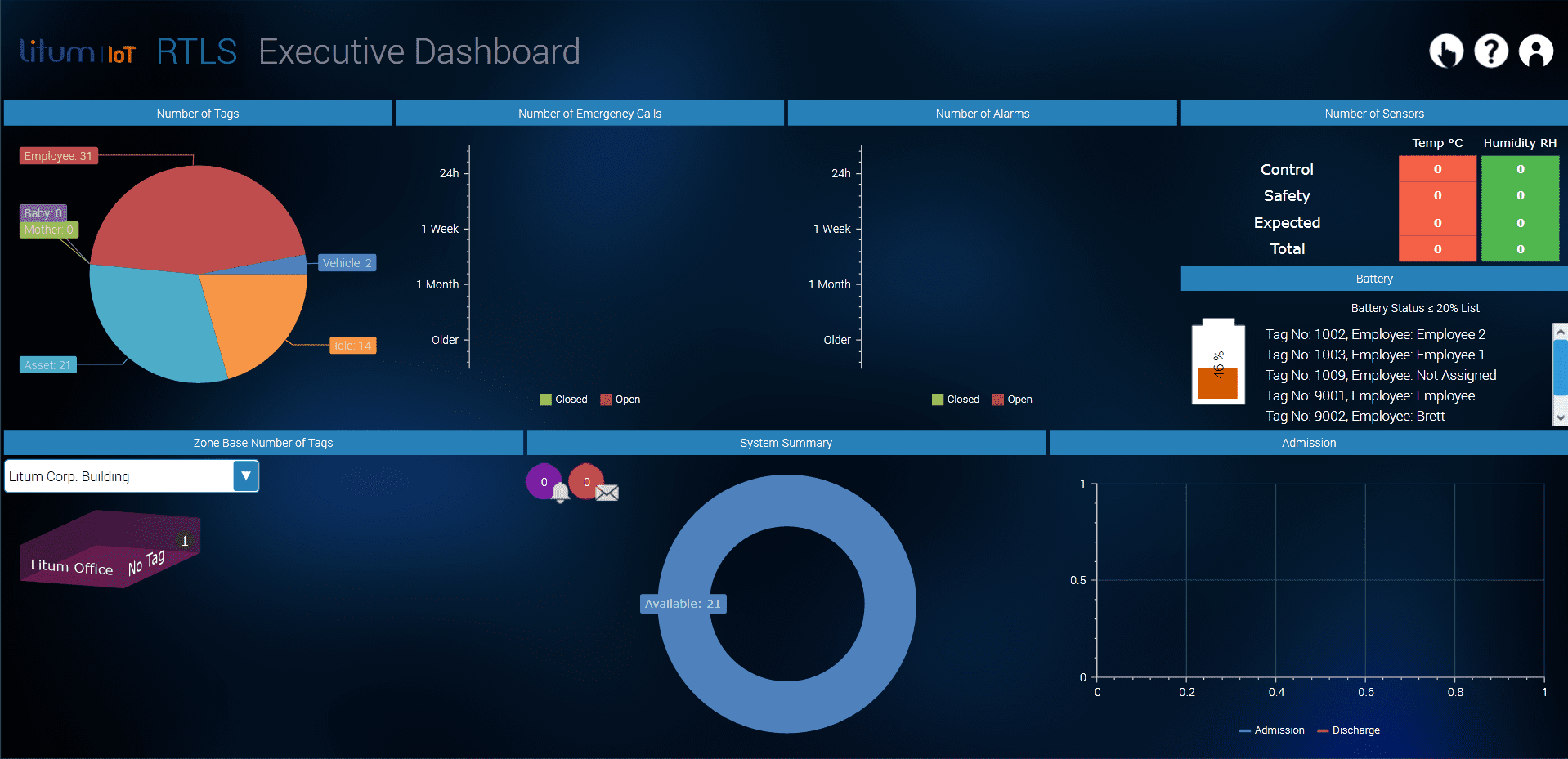
Of course, the data captured in Litum IoT sensors for delivered equipment and material as well as the other data for the same equipment and material captured in PMWeb can be used to develop a report that could be needed by other project stakeholders who need information on the stored assets but without the other details available in Litum Dashboard. MS Power BI can be used to visualize and report on this information in the desired layout and format. For example, a report can be created that will show the layout for each storage location, a log of all stored assets at the location, a visual to summarize stored assets by specification group, and filters to query the stored assets by manufacture name, asset name, delivery time frame, inspector who inspected delivered assets among
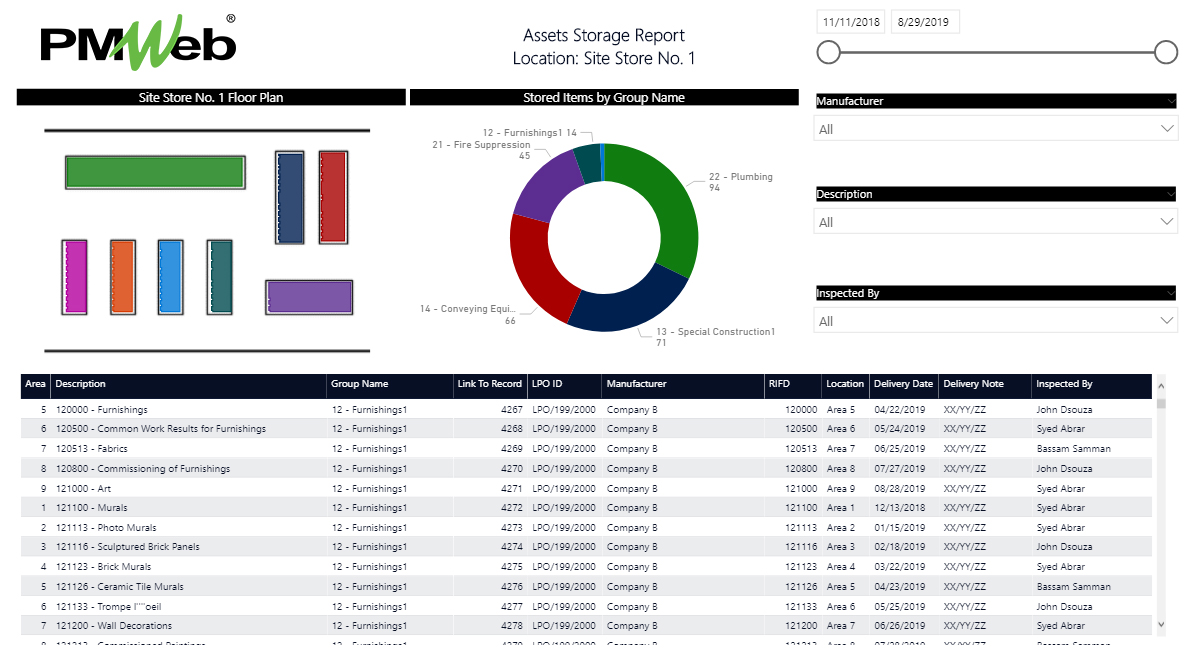