One of the quality controls processes that exists on any construction project for which a project control system (PCS) reports is the Punch List or Snag List. The traditional approach to using this quality control process is to use it when the project reaches the stage that is considered to besubstantially completed and for the project owner instructs the engineer to do the final inspection of the completed works to determine work itemsthat need to be rectified by the contractor before it can be accepted to be turned over to the project owner. The contractor is given a specified period to do those rectifications otherwise the project owner can deduct monies from the contractor’s contract and get other contractors to do therectification works. A Punch or Snag List is neither a Work Inspection Request (WIR) nor a Non-Compliance Report.
The other approach for using the Punch List or Snag List is as an Observation Report where the project owner and his team proactively capture andreport the details of all work items that need to be rectified by the contractor. The content of the Observation Report is captured in a real-time report that is shared by the contractor. This helps in reducing the work items that need to be rectified when the project reaches the substantial completionstage.
The PMWeb Snag List module allows project team members to create an unlimited number of snag lists. Documents and pictures relevant to what has been inspected get attached to the snag list. The PMWeb Viewer is used to view these documents and provides an option to add comments to these documents. Pictures and videos may be taken and attached to the template if the snag list is accessed through a smart mobile device.
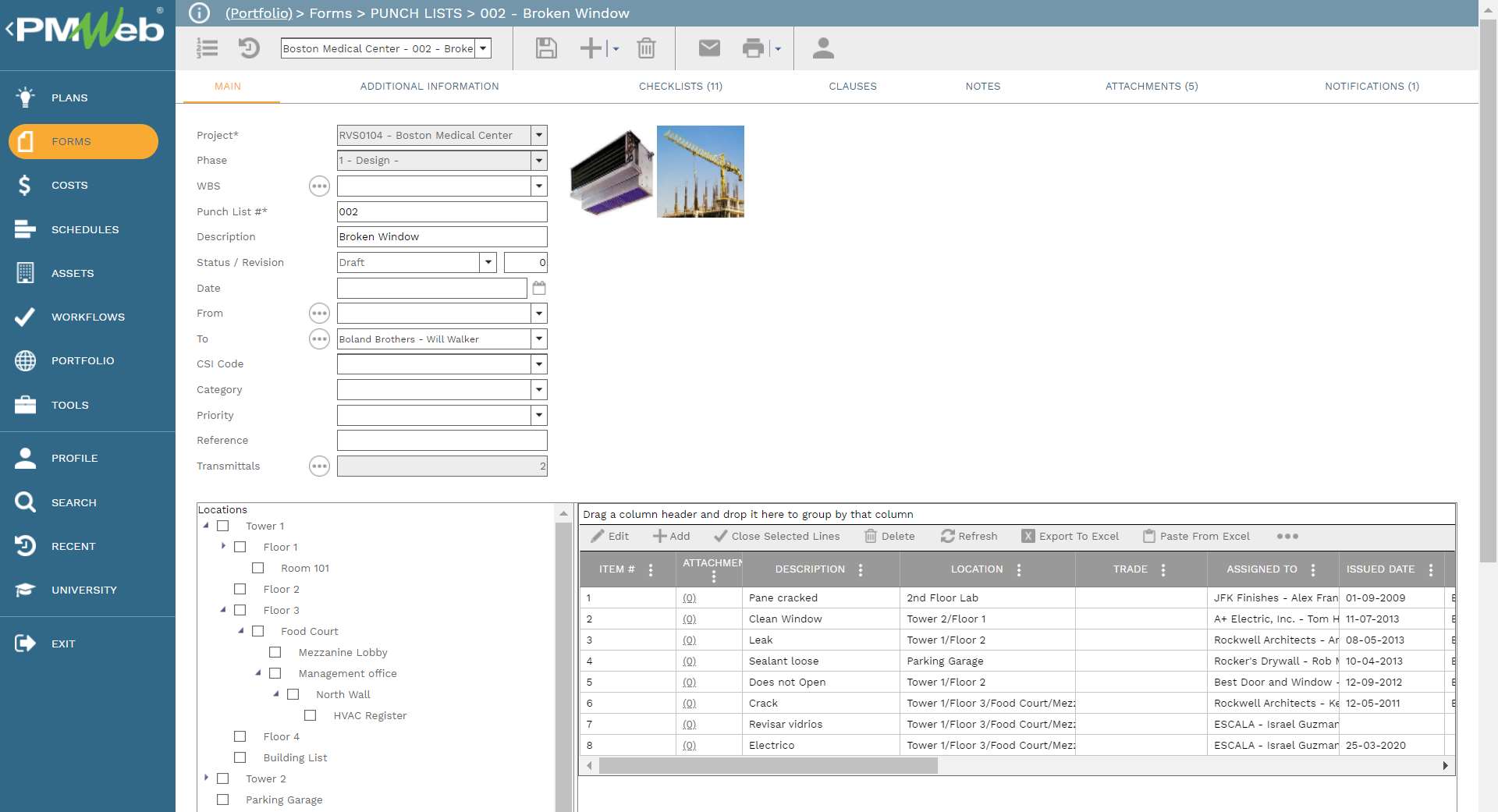
All documents and pictures attached to the snag list also become available to view. The PMWeb Viewer can also add comments and remarks to these documents when needed. The project team can append the attachment list with other documents, other PMWeb records, and imported email communications. To ensure the snag list is distributed to the right project team members, which usually includes the contractor and other stakeholders who must be kept informed of the reported defects and omissions, a workflow can be pre-defined to include all the review approval tasks. PMWeb allows capturing the actual dates for performing those tasks and comments made by each reviewer.
In addition, PMWeb provides the option for capturing punch list items using PMWeb Mobile App. Each punch list item needs to capture the name assigned to the register, by whom the punch list items were captured, and to which contractor, subcontractor, or supplier the punch list relates.
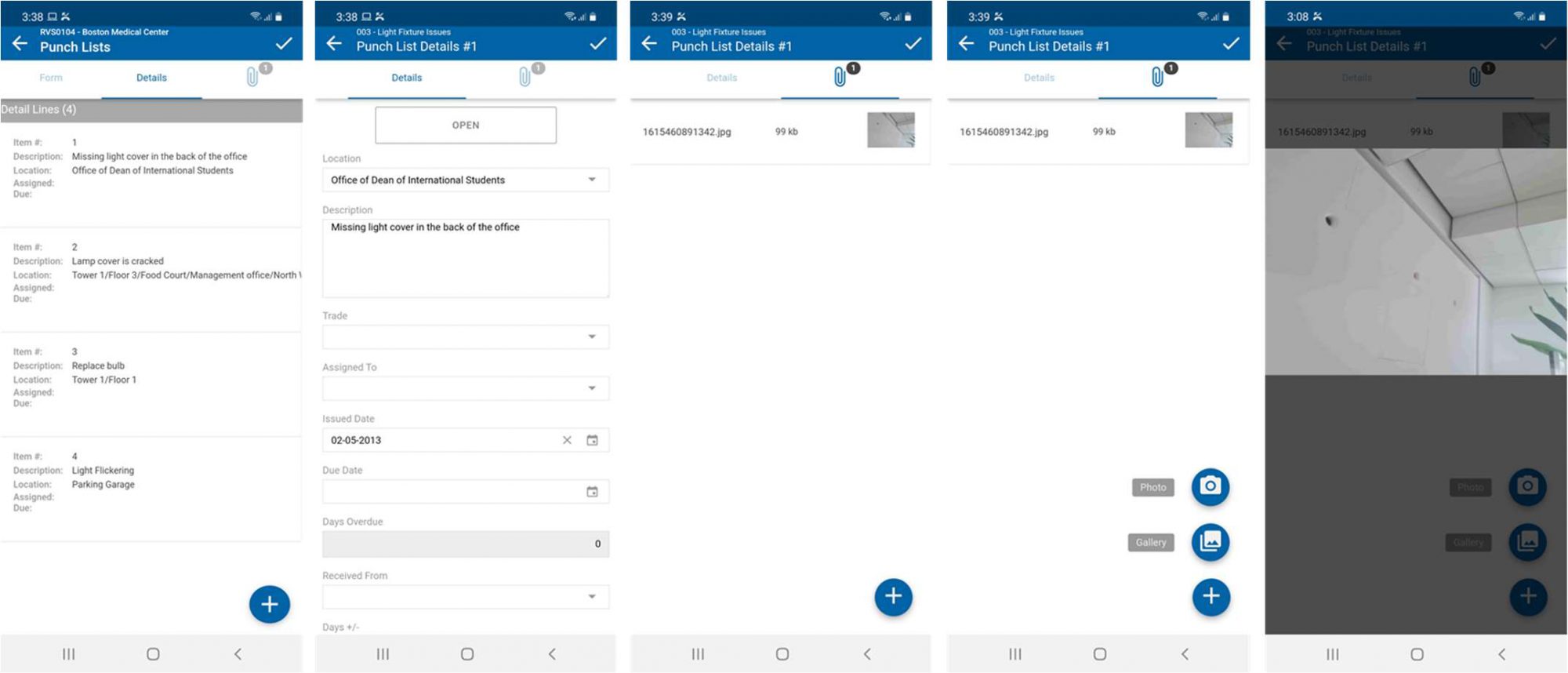
The defects and omissions reported by the different project team members become available for the project manager to report on in various forms and formats. These reported defects and omissions can be grouped by their work category, location, who reported them, whose responsibility it is to rectify, number of overdue defects and omissions, and any other attribute used while capturing this information.
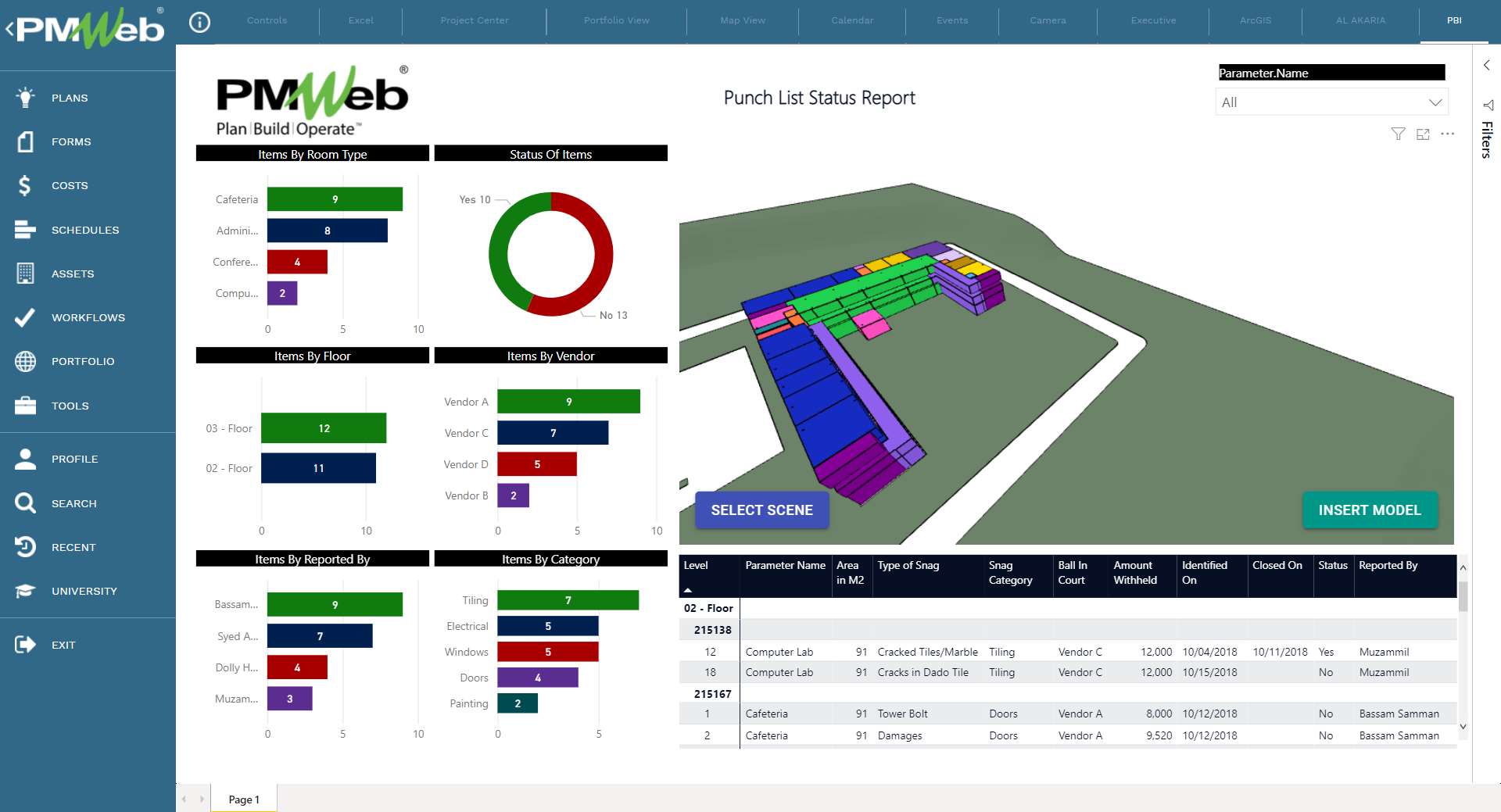
Reference
The content of this article was extracted from the book titled “Let’s Transform: Enabling Digital Transformation of Capital Construction ProjectsUsing the PMWeb Project Management Information System – 2nd Edition” written by Bassam Samman.
The book provides project owners with oversight on how technology available today can support their efforts to digitally transform the management of their projects’ portfolios. For each capital project life cycle stage, PMWeb is used to detail how the relevant project management business processes can be digitalized to enforce transparency and accountability in delivering projects. In addition, MS Power BI was used to show how the real-time, trustworthy data captured in PMWeb can be aggregated, modeled, monitored, evaluated, analyzed, and reported at anytime,anywhere using any device.