All professionals who are either involved or have been involved with project controls know that planning and scheduling were the starting point for the evolution of the project control practice. This is managed under the Schedule and Resource Management module of a project control system.
The Schedule and Resource Management module has at least five important functions to achieve. The first of those requirements is the submission and approval of the baseline resource-loaded schedule developed by the planning and scheduling team. The second function is the use of this schedule to execute the project’s activities and capture the actual progress needed to update the schedule. The third function is to ensure the validity of the required resources to perform the project schedule activities which become the basis for determining the resources required for the project. In addition, capturing the actual resources spent on performing the project schedule activities and comparing them to what was planned in the schedule, booked resources, and actual resources charged to the project. This information provides the input for the fourth function which has to do with productivity analysis and reporting for the project’s key trades. The fourth function includes capturing details on the disruptions, delays, and associated extension of time requests and time impact analysis. The last and fifth function is the reporting associated with the schedule and resource management module.
In construction projects, there are at least five levels for the project schedule. The first level is also known as the Overall Strategic Plan or the Projects Portfolio schedule whereas the second level is known as the Master Control Schedule or Program Schedule. The third level is the Integrated Schedule, while level four is the Work Package Schedule or the Consultants and Contractors Schedule, which is usually resource-loaded. The last level, level five, is the detailed schedule level. Some organizations use MS Excel to create this detailed level, which is not a recommended practice.
The level four schedule details the activities needed to execute the control accounts or work packages for the project. Those include the management control points where the integration of scope, budget, actual cost, and schedule takes place, and where the measurement of performance occurs. Each control account or work package associates with a specific single organizational component in the organizational breakdown structure (OBS). In a construction project, there could be engineering (EWP), procurement (PWP), construction (CWP), and startup (SWP) work packages. The startup work packages (SWP), also sometimes named turnover work packages (TOP), include the scope of work for testing and commissioning activities.
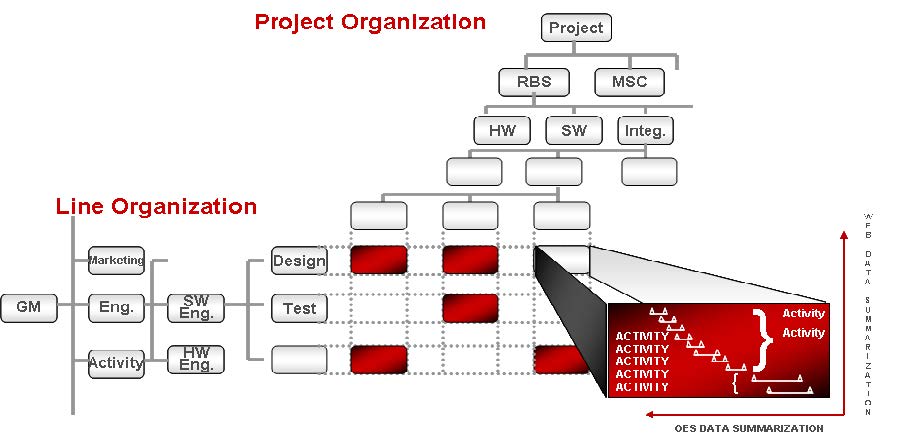
The level four schedule is created by the engineering consultants and contractors appointed by the project owner. The engineering consultants’ schedule includes the activities needed to produce the engineering deliverables included in the Engineering Work Packages (EWP). On the other hand, the contractors’ schedules include the activities for site mobilization, technical submittals, procurement, construction and installation, and testing and commissioning activities. These are activities needed to produce the deliverables included in the procurement (PWP), construction (CWP), and startup (SWP) work packages.
The level activities’ detail for the level four schedule is the level where activities can be assigned and clearly defined, the duration can be estimated, labor and non-labor resources can be estimated, the cost can be estimated and progress can be tracked. For construction projects, the duration of a construction or installation activity should not exceed ten working days.
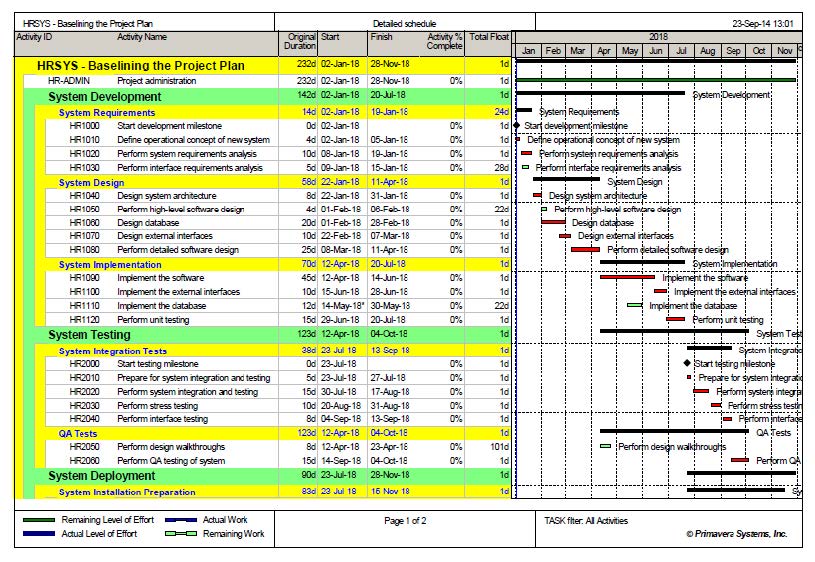
In addition, the duration of each activity needs to be estimated based on estimated work and historical productivity rates. Great care should be given to avoid the risk of underestimating the activities’ duration. This is usually caused by the planners being optimistic and desiring to please senior management, underestimating nonproductive periods, incomplete recall of the previous experience, unfamiliar with the complete project scope, and no experience in specific activities needed for the project.
Further, the productivity or production rates used to estimate the activities need to be realistic and valid for the project. In general, the production rate should be the planned average daily production rate based on the available resources and the environment within which the work is performed. It also includes the idle and nonproductive time associated with the movement and set up of equipment, break times, expected equipment downtime for maintenance and repair, and other expected downtime.
The project planning engineers should analyze and consider the different factors that could impact the production rates. Examples of those factors include the nature of the work to be performed, labor and equipment productivity rates, project management skills, material and equipment availability, seasonal conditions, work restrictions, the required quality of work, concurrent activities, interfaces with other contractors, and others.
The project schedule also identifies the dependencies between the activities. There are three sources for dependencies. The first is known as mandatory or hard logic which is inherited like the work being done (e.g., you must design before you can construct). Whereas the second source is known as discretionary or preferred, preferential or soft logic which is based on experience, desire, or preferences. The third and last source is external which is based on the needs or desire of a party outside the project (e.g., government or suppliers).
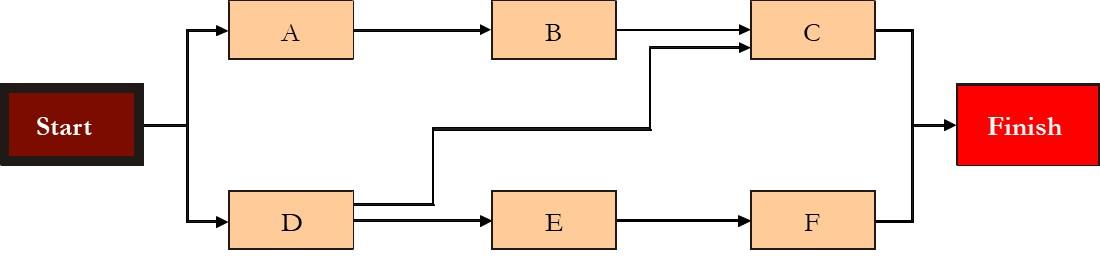
This enables calculating the project’s schedule start and finish dates using the Critical Path Method (CPM). The forward pass analysis starts at the beginning (left) of the network and develop an early start and early finish date for each activity, progressing to the end (right-most box) of the activities network. The Early Start Date (ES) is the earliest possible point in time an activity can start, based on the network logic and any schedule constraints whereas the Early Finish Date (EF) is earliest possible time the activity can finish.
The backward pass calculates the late start and late finish dates by starting at project completion, using finish times, and working backward. The Late Start (LS) date is the latest point in time that an activity may begin without delaying that activity’s successor. If the activity is on the critical path, the project end date will be affected. On the other hand, the Late Finish (LF) date is the latest point in time a task may be completed without delaying that activity’s successor. If the activity is on the critical path, the project end date will be affected.
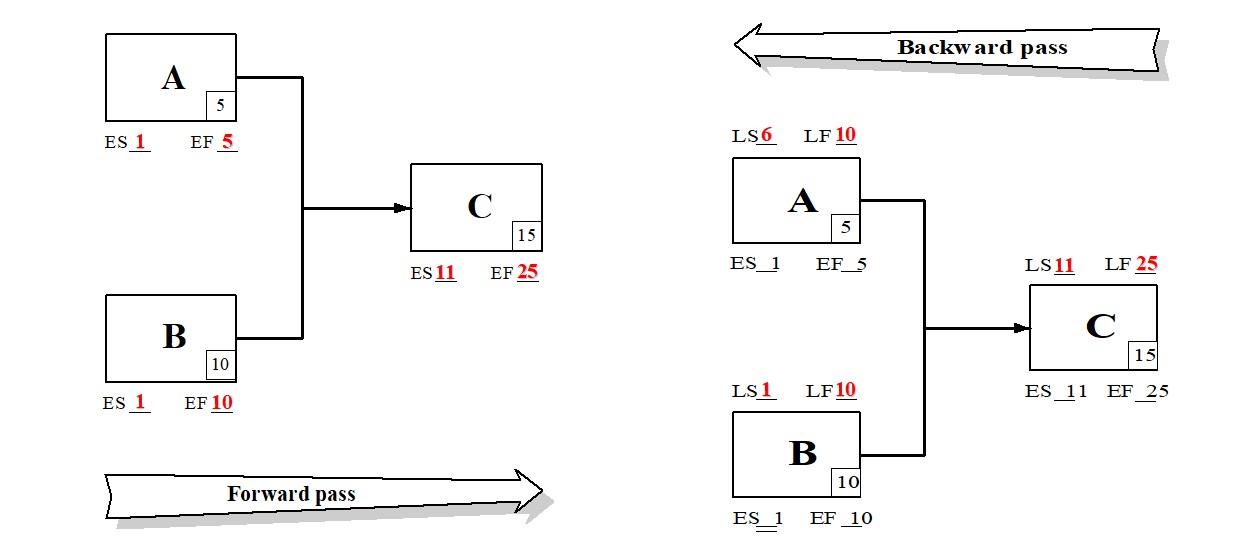
The early and late start and finish dates become the basis for calculating the Total Float (TF) for each activity. The Total Float is the amount of time an activity can slip from its early start without delaying the project which is the difference between an activity’s late dates and early dates.
Activities with zero total float are known as critical activities for which the critical path is the longest duration path through a network diagram and determines the shortest time to complete the project. Activities could have zero, positive, and negative float. A positive float is when an activity’s early finish date is earlier than the activity’s late finish date. On the other hand, a negative float is when the activity’s late finish date needs to be earlier than the activity’s finish date. This would happen when the project’s delayed due to a constraint. This constraint could be either a “Finish No Later” constraint or a “Finish On” constraint.
When developing the project’s schedule, there could be a need to use Date Constraints. They constrain the scheduling of activities during the forward (early date constraints) and backward (late date constraints) passes based on calendar dates. Date constraints take precedence over schedule when performing schedule calculations.
Date Constraints are used to impose date restrictions which reflect project requirements that cannot be built into the logic. This makes the project schedule more accurately reflect the real-world aspects of the project, provide additional control to the project, and impose a restriction on the entire project or an individual activity. Examples of Date Constraints include Start On, Start No Later, Start No Earlier, Mandatory Start, Finish On, Finish No Later, and Finish No Earlier.
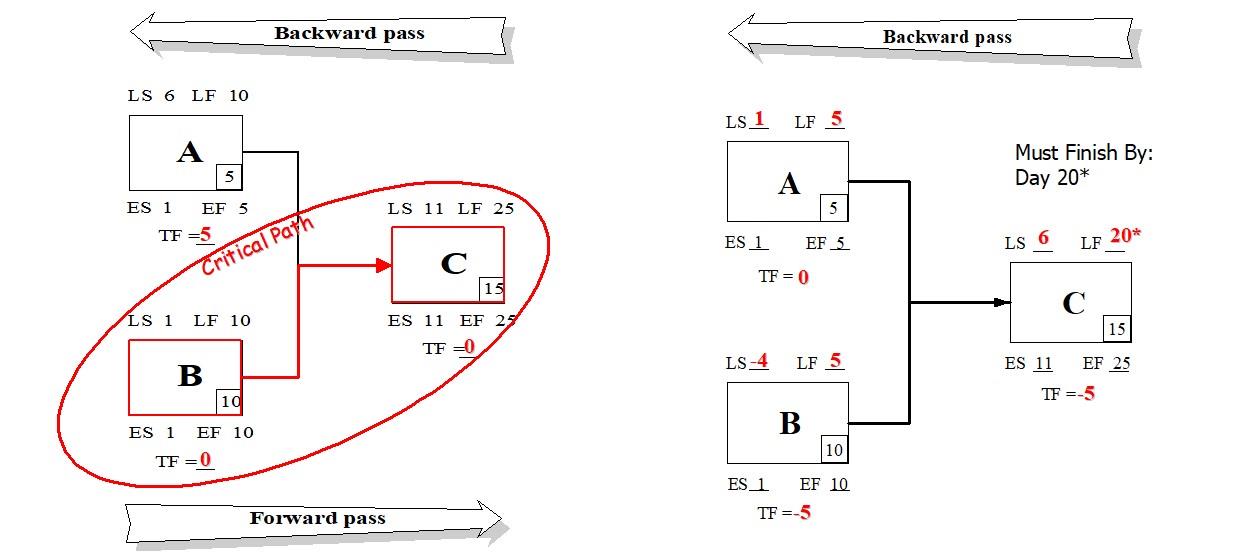
Reference
The content of this article was extracted from the book titled “Let’s Transform: Enabling Digital Transformation of Capital Construction Projects Using the PMWeb Project Management Information System – 2nd Edition”. The book was written by the author of the posted article, Bassam Samman.
The book provides project owners with oversight on how technology available today can support their efforts to digitally transform the management of their projects’ portfolios. For each capital project life cycle stage, PMWeb is used to detail how the relevant project management business processes can be digitalized to enforce transparency and accountability in delivering projects. In addition, MS Power BI was used to show how the real-time, trustworthy data captured in PMWeb can be aggregated, modeled, monitored, evaluated, analyzed, and reported at anytime, anywhere using any device.